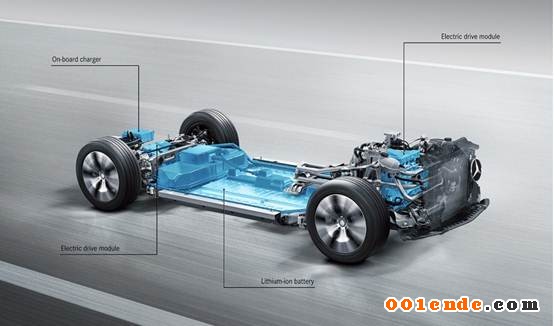
圖1德國奔馳汽車的純電動汽車架構(gòu)MEA (Mercdes-Benz Electric Car Architecture)(圖片來自“Motor Authority” 2016.06.13)
2008年世界經(jīng)濟危機后的汽車工業(yè),痛定思痛,各大企業(yè)都在尋找突破困境、可持續(xù)性發(fā)展的道路:
●2009年,德國奔馳汽車首先提出模塊化戰(zhàn)略(Modulstrategie), 定義出Mercedes-Benz Front-Wheel-Drive Architecture(MFA)和Mercedes-Benz Rear-Wheel-Drive Architecture(MRA)的整車架構(gòu)。核心目的就是要在150億歐元的年采購總額中,降低成本20%(30億)歐元
●2010年至2015年間,大眾汽車也提出車型平臺化,計劃了Modulare Querbaukasten (MQB)和Modulare Längsbaukasten (MLB); 寶馬汽車公布了FWD (Front-Wheel-Drive)和RWD(Rear-Wheel-Drive)的整車架構(gòu);2015年3月27日,豐田汽車也宣布了TNGA(Toyota New Global Architecture)整車架構(gòu),目的要降低25%的研發(fā)成本
為什么這些先進的大型汽車企業(yè),紛紛提出模塊化、整車架構(gòu)?這里首先要從零部件的成本和需求量的解析關(guān)系說起:
每一個零部件,都有它相應(yīng)的生產(chǎn)線及生產(chǎn)設(shè)備,當這條生產(chǎn)線全年滿負荷生產(chǎn)時,零部件單件成本指數(shù)為1,單件成本指數(shù)和產(chǎn)量有如下的解析函數(shù)關(guān)系:
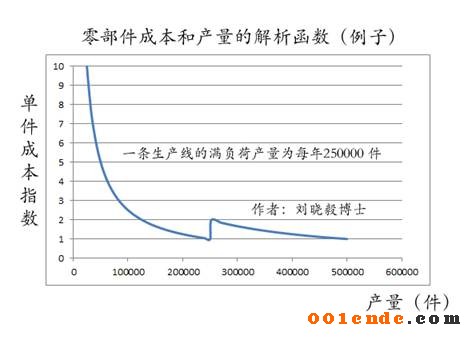
圖2 零部件單件成本指數(shù)和產(chǎn)量的解析函數(shù)關(guān)系(劉曉毅博士首次提出的成本工程理論)
也就是說,產(chǎn)量的增加,使零部件的單件成本降低,其主要原因是生產(chǎn)線的投資總額可以分攤到更多的零部件上了;產(chǎn)量需求超過了一條生產(chǎn)線的產(chǎn)能,增加的第二條生產(chǎn)線,將導致解析函數(shù)的跳越(見圖2)。這就是為什么要模塊化、共通化的主要原因了,一個零部件如果不只是用在一個車型上,而是用在多個車型上,它的需求量就大幅增加,單件成本也就降低了。
以此為基礎(chǔ),這里就深入地介紹一下作者參與的奔馳模塊化戰(zhàn)略的經(jīng)歷:
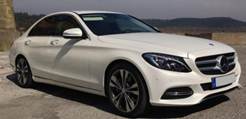
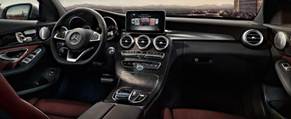
圖3 奔馳C級轎車(W205)(圖片來自奔馳官網(wǎng))
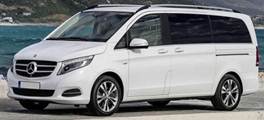
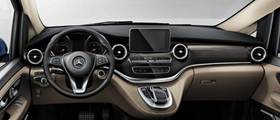
圖4 奔馳V級MPV(VS20)(圖片來自奔馳官網(wǎng))
圖3和圖4這兩款車型,外觀、尺寸大不一樣,但是,如果仔細觀察一下內(nèi)飾,不難發(fā)現(xiàn),許多零部件、系統(tǒng)是一樣的(或幾乎是一樣的),比如方向盤、儀表盤、導航儀、中央控制單元(Zentralbedieneinheit)和Touchpad,空調(diào)出風口,電子開關(guān)等等。這些,就是模塊化的系統(tǒng)和零部件,是在多款車型通用的,如果有細節(jié)的區(qū)別,通常是裝飾框、亮條,或表面處理不一樣而已,其核心系統(tǒng),是完全一樣的。
模塊化戰(zhàn)略,有如下的核心要點:
目的:
通過模塊化戰(zhàn)略,大規(guī)模降低模塊的單件成本(降低20%,總額30億歐元)
●降低eHPV(Engineered Hour per Vehicle, 設(shè)計出的單車制造時間),并使生產(chǎn)過程標準化(提高制造質(zhì)量,降低制造成本)
●降低研發(fā)成本,降低單車研發(fā)深度、減少研發(fā)風險
●降低整車重量,減少油耗(輕量化)
●提高整車可靠性和質(zhì)量
實施過程:
●針對所有的15款車型,每個車型統(tǒng)一按功能分解成90多個模塊
●對每個車型都做其兩個生命周期的模塊化定義并設(shè)定各模塊投入時間表
● 全集團共有約3000工程師,投入模塊化戰(zhàn)略過程中,為期18個月。共有90多個模塊小組,每個模塊小組由研發(fā)、成本、生產(chǎn)工藝、質(zhì)量工程師組成,每周兩次會議,周一是技術(shù)研討會,周三是跨部門課題會議
模塊化方法:
●在模塊化的18個月內(nèi),分為三個階段:模塊分析階段、戰(zhàn)略和技術(shù)方案階段、實施階段(因各個模塊開發(fā)周期不同,有不同的實施時間表)
●每一個階段,都用了大量標準化指導問題。分析和戰(zhàn)略技術(shù)方案過程中,對模塊功能定義、接口、成本、重量、可制造性、供應(yīng)鏈都應(yīng)用了各類方法、數(shù)據(jù)庫,以達到性能、成本、重量、質(zhì)量綜合最優(yōu)的技術(shù)方案
這里涉及許多的方法、流程、模塊化戰(zhàn)略運作模式的細節(jié),作者就不作一一描述。
總之,
Ø 模塊化戰(zhàn)略是汽車企業(yè)的未來核心工作,無論是常規(guī)動力的車型,還是新能源車型的研發(fā),無論是數(shù)字化、無人駕駛,還是共享車型(奔馳提出的CASE: connected, autonomous, shared, electric),從產(chǎn)品定義、系列開發(fā)、直至量產(chǎn),需要貫通模塊化戰(zhàn)略至每個車型的兩個生命周期
Ø 模塊化戰(zhàn)略是德國工業(yè)4.0(中國制造2025)的重要組成部分
Ø 模塊化戰(zhàn)略可以大規(guī)模降低汽車企業(yè)的產(chǎn)品成本15%-20%,它不是從單一車型甚至單個零部件著手,而是從所有車型統(tǒng)籌、全體的成本企劃,所以,模塊化戰(zhàn)略也是成本工程2.0!
Ø 模塊化戰(zhàn)略可以降低研發(fā)成本、縮短研發(fā)周期,減低研發(fā)風險,同時提高車型的可靠性和質(zhì)量
Ø 模塊化戰(zhàn)略也可以應(yīng)用到汽車零部件供應(yīng)商企業(yè),這里的方法、運作模式是可以借鑒的
Ø 中國的汽車企業(yè),還處在成本工程1.0的初期,有的企業(yè)甚至還沒有成本工程。企業(yè)所有車型的模塊化戰(zhàn)略提到議事日程上了嗎?何時能進入到成本工程2.0?“比你優(yōu)秀的,比你還努力”!加油吧,中國的汽車企業(yè)和汽車工程師們!
作者劉曉毅博士(觀昱機電技術(shù)(CostKey-Solutions)創(chuàng)始人),德國戴姆勒集團(奔馳汽車)21年的資深汽車技術(shù)經(jīng)驗(動力總成電子控制系統(tǒng)系列開發(fā)、整車企劃、成本工程、新工藝開發(fā)、變速箱生產(chǎn)等部門高級經(jīng)理),主導過奔馳汽車重卡16擋自動化變速箱系列開發(fā)、動力總成零部件和空客大型結(jié)構(gòu)件的新工藝開發(fā)、電動商務(wù)車整車和成本企劃、商務(wù)車及轎車的多項降低成本重點項目(PKO/OPTIMA,CTX, CORE)。長城汽車技術(shù)中心擔任高層技術(shù)管理,為長城汽車集團組建了中國車企第一個全建制的成本工程體系、方法和流程,并使它融入了集團的整個產(chǎn)品過程。